Banshee
Moderator
- Joined
- Jul 24, 2012
- Messages
- 13,516
I took a stroll through Warwick yesterday afternoon to pick up my Kunifer fuel pipe.
I've got 7.5 metres of both 6mm & 8mm and ready to get it fitted to the truck but I wanted some tips on how I should be bending, flaring etc.
I managed to remove both the feed and return in one piece intact. I planned on getting a length of Kunifer straightened out to just a tad longer than the original pipe, put it next to each other and use the pipe bender I've ordered to follow the angles of the original pipe, once that section is done I was going to wrap them together tight as I can with some electrical tape and work my way to the end.
I'm really surprised how bad the pipes were as they didn't look too bad when I waxoyled them last time around but that was a while ago, I'm just glad the chassis and body are not in the same state
They seem to be worse where they have been clamped, I'm not using the original fixings again I've purchased some rubberised "P" clips in both 8mm and 6mm and will use according along the chassis.
I've got 7.5 metres of both 6mm & 8mm and ready to get it fitted to the truck but I wanted some tips on how I should be bending, flaring etc.
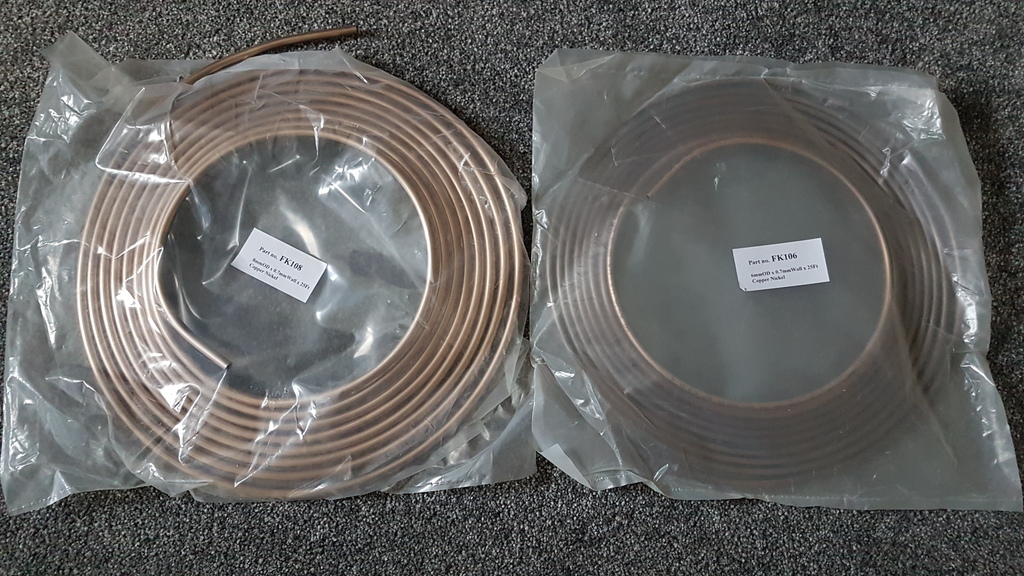
I managed to remove both the feed and return in one piece intact. I planned on getting a length of Kunifer straightened out to just a tad longer than the original pipe, put it next to each other and use the pipe bender I've ordered to follow the angles of the original pipe, once that section is done I was going to wrap them together tight as I can with some electrical tape and work my way to the end.
I'm really surprised how bad the pipes were as they didn't look too bad when I waxoyled them last time around but that was a while ago, I'm just glad the chassis and body are not in the same state
They seem to be worse where they have been clamped, I'm not using the original fixings again I've purchased some rubberised "P" clips in both 8mm and 6mm and will use according along the chassis.
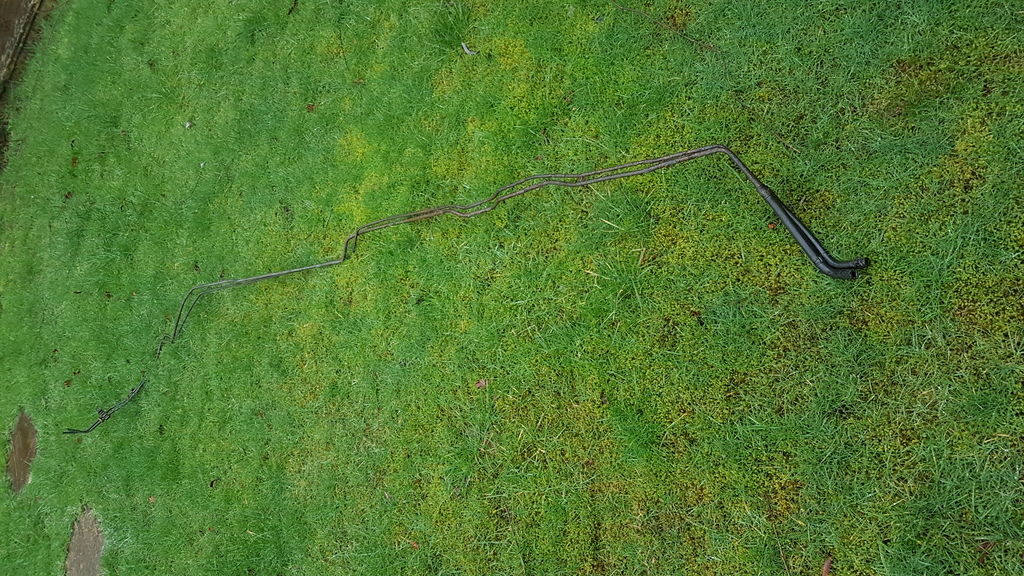
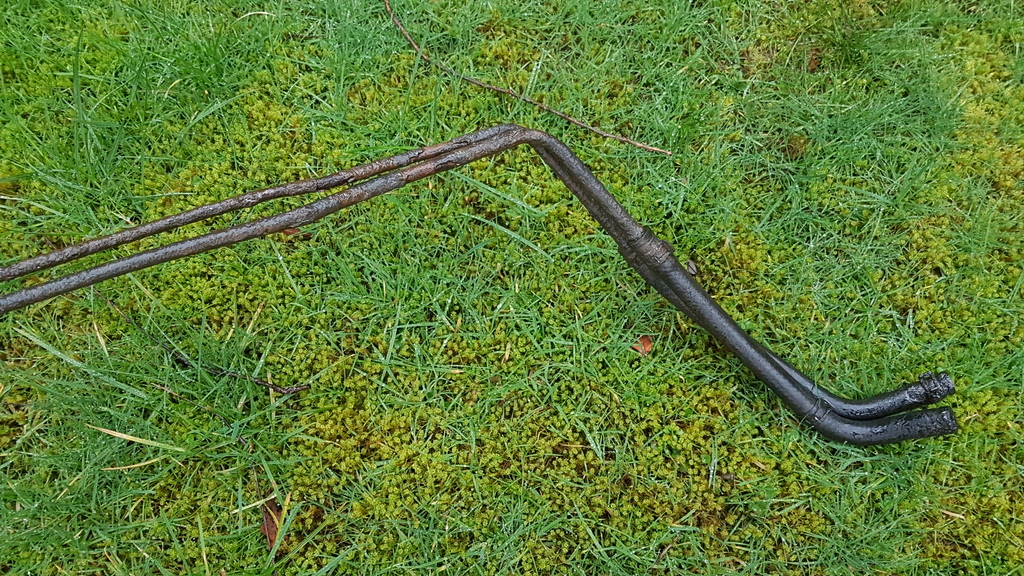
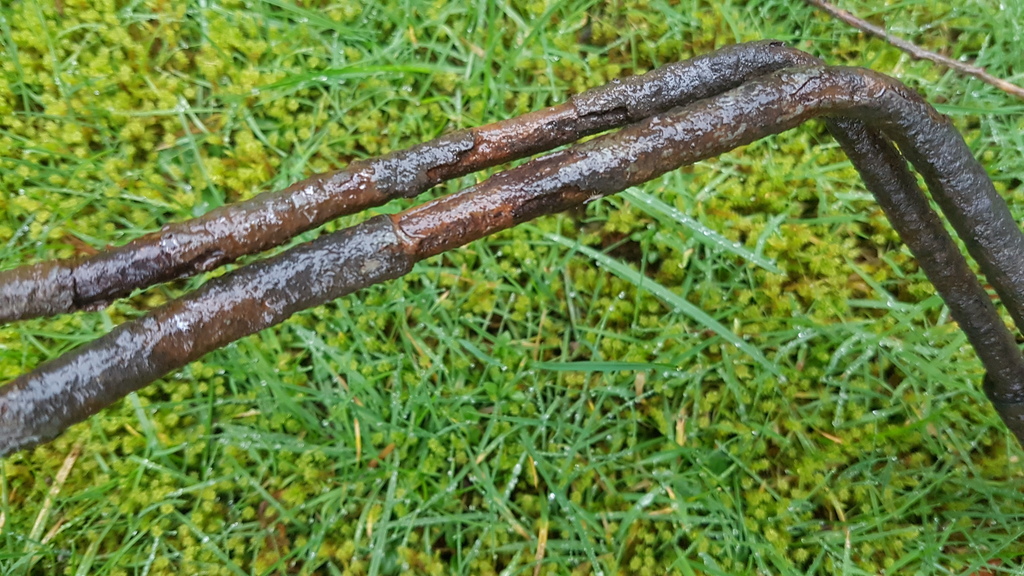
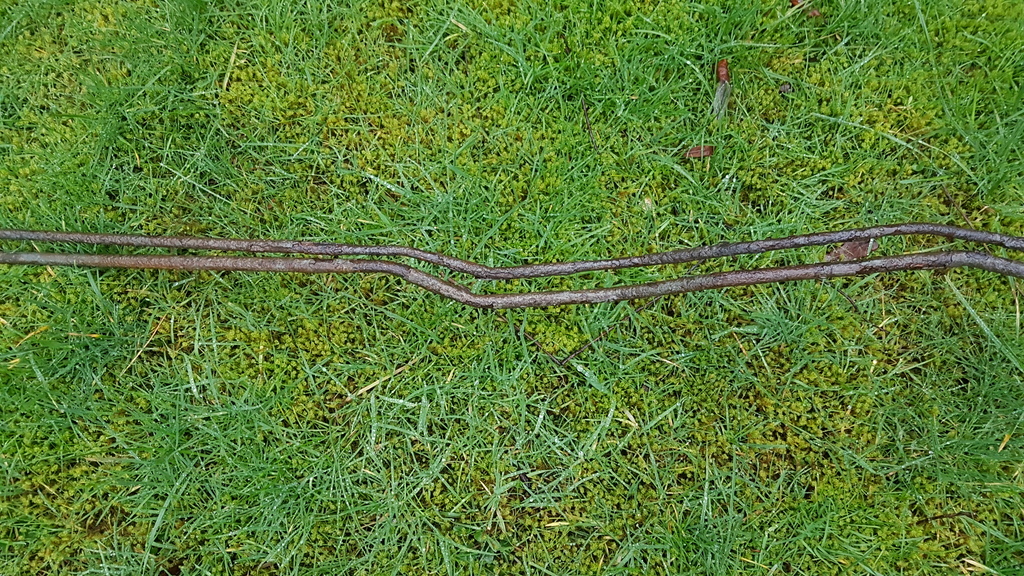
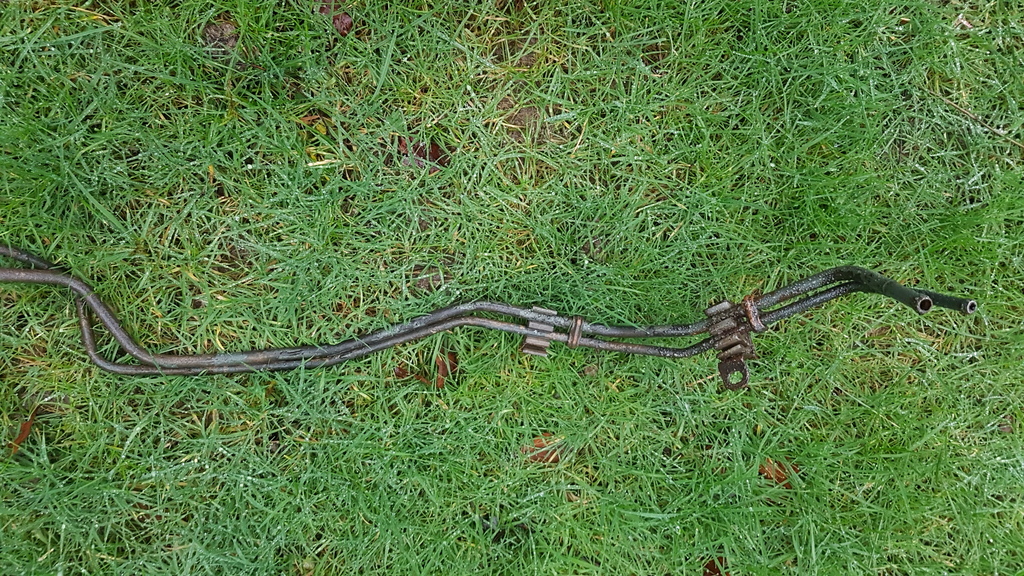
Last edited: